Specialist Services has successfully completed the ETR and ICR Buildings project awarded by Tecnicas Reunidas
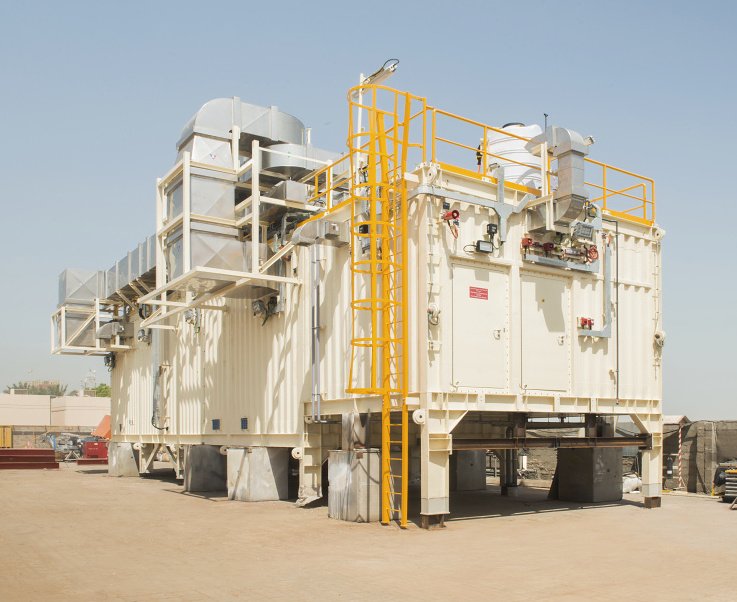
Tecnicas Reunidas (TR) awarded Specialist Services the contract for the supply of an Electrical Technical Room (ETR) and an Instrument Control Room (ICR) to be used on the ADOC’s Hail Oil Field offshore Abu Dhabi.
Project: Supply of ETR and ICR buildings for Hail Oil Field Development Project
Client: Tecnicas Reunidas
End User: Abu Dhabi Oil Company – ADOC
Location: Hail Oil Field offshore Abu Dhabi
Project Completion: 17th April 2017
ETR dimensions: (L) 34 x (W) 11 x (H) 10.8 m
ICR dimensions: (L) 21 x (W) 8.3 x (H) 9.4 m
Project requirements
Abu Dhabi Oil Company (ADOC) intend to develop the Hail Oil Field located approximately 10km South of Mubarraz Island in the shallow water areas of the Arabian Gulf and 100km West of Abu Dhabi. This development aims to achieve a peak in oil production of 21,000 BPD from the Hail Oil Field. The oil shall be produced from the Thamama Zone A, B and F reservoirs and require some gas injection and gas lift for oil recovery. Tecnicas Reunidas (TR) had been awarded a project of the Hail Oil Field development Early Production Scheme (EPS) phase.
In order to facilitate the above, the prefabricated containerised type Electrical Technical Room (ETR) and Instrument Control Room (ICR) were required and TR awarded the project to Specialist Services. The scope of work included design, engineering, manufacturing, installation of equipment, interconnection cabling, inspection, testing, pre-commissioning, packing, shipping and supply of ETR and ICR buildings.
The buildings were required to be prefabricated, self-contained, skid-mounted, factory manufactured, completely assembled, wired and tested at the factory prior to being mobilised to the site. Other requirements included the provision of the HVAC system, for the buildings mounted on skids in non-hazardous areas, false floors, HSSD and NOVEC Firefighting systems, a minimum of 2 hours fire rating for external walls, roof, floor and doors, and also to be blast-resistant.
Solution
The ETR and ICR buildings have been designed, manufactured and supplied in line with ADOC’s requirements. At the beginning, our engineering team worked exceptionally hard to engineer the solutions that would satisfy client’s specifications, and additional design change requests from the client were also successfully implemented during project execution.
The structural design of the buildings was frozen by the end of October 2016. Detailed engineering and fabrication had to be done in tandem to complete the project on time, as required by the contractor at Hail Field. We timely achieved this through close cooperation with the contractor and third party inspectors.
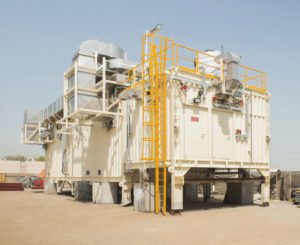
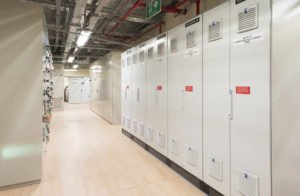
The project was challenging due to the unusual completion schedule for both buildings: 22 weeks for ICR and 26 weeks for ETR. Specialist Services Mussafah yard team in Abu Dhabi worked tirelessly for three months to complete the project in this short lead time, demonstrating outstanding dedication and excellent work.
In-land transportation of ETR to Mussafah Port Jetty was a major challenge due to its width and height. However, Specialist Services, together with their transporter, managed the operation well with proper planning and utmost care. Prior permissions from Abu Dhabi Municipality, Road Transport, Traffic and Mussafah Port authorities were obtained for smooth operations.
Conclusion
The project required complex engineering, coordination and construction due to the specific requirements related with existing interfaces and characteristics of the Hail Oil Field Terminal. A number of specifications and design changes were requested by the client, which resulted in additional works.
The pre-commissioning of the installed systems lasted around 20 days under close vigilance and inspection by TR, Mott MacDonald (PMC) and ADOC staff deployed at the Specialist Services yard in Abu Dhabi.
After a successful site acceptance test of the ETR and ICR buildings by TR and ADOC, these heavy structures were weighed using hydraulic jacks & load cells arrangement at the Specialist Services yard in Abu Dhabi. ICR weighing operation was carried out on 13th April 2017 using 10 load cells, while ETR used 18 load cells on 16th April 2017. ICR and ETR weighed 114 Ton and 237 Ton respectively.
We completed the project and handed it over to TR at Mussafah Port Jetty, Abu Dhabi, on 16th and 17th April 2017 in line with the agreed completion schedule. Both buildings were transported to Mussafah Port with the help of SPMTs in-land transportation.